JP01 - Arisu Custom CNC Aluminum Unibody Keyboard Case
https://youtu.be/O6BLock8iVU
https://youtu.be/mfLEsenbGh8
This repository all assets needed to manufacture a custom high-quality CNC milled unibody keyboard case for the open source Arisu PCB. I'm very pleased how the first prototypes came out and I'm documenting the entire process here.
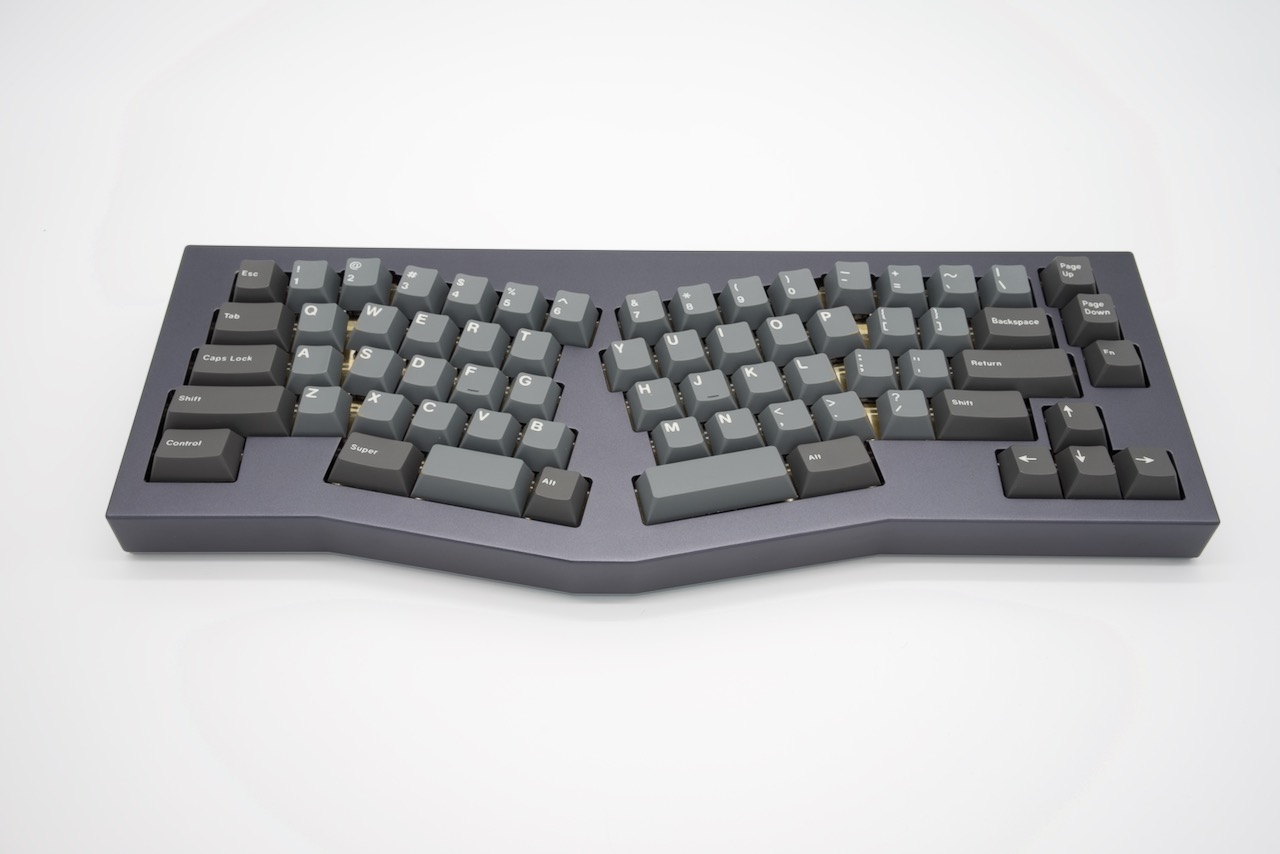
CAD screenshots:
![]() |
![]() |
![]() |
![]() |
![]() |
![]() |
More images from the first complete build (Not renders but an actual build Show Me The Build!):
![]() |
![]() |
![]() |
![]() |
![]() |
![]() |
![]() |
![]() |
![]() |
Test assembly and parts:
![]() |
![]() |
![]() |
![]() |
![]() |
![]() |
Goals
- Opensource all of my assets and show how "easy" it is to build a custom case in the hopes to inspire more who are interested in the challenge
- Attain a specific aesthetic drawing inspiration from countless custom keyboard case designs from the community, but none of which hit the mark for me
- Build on the opensource Arisu PCB layout which I find to be close to perfect and build a case that can do it justice. Once I saw the Arisu PCB layout I knew what I needed to do
- Build the model in the OnShape CAD platform which is completely free for non-commercial projects making this even more accessible to others
- If you order all of the parts at the same time, you can have a fully functioning high-quality custom keyboard in less than a month. No need to waiting for a group buy, not getting the custom color you want, etc.
- With the first prototype I aimed for a quiet keyboard that still has the best mechanical feel while being silent enough to not be invasive to others yet still a pleasing sound
- Provide not only high-fidelity .STEP model files, but also drawings to accompany them to help ensure you get what you order. Some shops prefer drawings over model files and I'm still stuck on the requirement that the manufacturer should be able to build your product solely from the drawings. My drawings are far from professional quality and I make no claims in being a professional
TL;DR
If you want to dive right into the models using OnShape: JP01 - CNC Unibody Case - Arisu Keyboard V1.1
Check out `Assets`_ If you want to explore models in other CAD platforms
How do I get this now?
- First understand the Risks
- Then check out Tutorial on Ordering Parts
But Why?
There are several prototype cases for the Arisu PCB in the works by some very talented individuals, but the challenge of building one from scratch to meet my design aesthetic was all too enticing.
What I'm looking for in a keyboard and why I think the Arisu layout is a worthwhile investment:
- QMK
- ANSI layout
- Split-fixed with ~18% ergonomic split angle
- Number row is a "must"
- Arrow keys are a "must". No special layers. No HJKL bindings. Just simple, yet present, arrow keys.
- No function rows, I stopped using them long ago
- Less control/super/alt modifiers
Specifications
- Unibody caseNo ugly seam to look at. Minimal fillet and small radii for a specific aesthetic. Simpler design to limit the number of individual parts to get CNC milled.
- 6061-T6 Aluminum
- Bead blasted with finer #150 grit
- Anodized matte finish
- Color: RAL 7024 (Graphite Gray)
- No special masking but instructions for not anodizing threaded holes on drawings
- Threaded holes for base plate and switch plate all M2.5x0.45 with anotation included in Drawings
- Dimensions359mm wide, 142mm deep, 31.9 mm high on back, 22mm high on frontThis is Very similar to stock Arisu case
- Weight ~4lb
- Typing angle 5 degrees
- Flat baseplateOriginal design is for a flat base plate that is slightly recessed into the case. I have incorporated my logo into the design with a 0.5mm depth and a 0.25mm fillet on the top edge
- 6061-T6 Aluminum
- Smoothed surface
- Anodized glossy finish
- Color: RAL 7001 (Silver Gray)
- No special masking but instructions for not anodizing threaded holes on drawings
- 4 through bolts to mate plate to case with for M2.5x0.45 countersunk screws
- Switch plate
- Top mount
- Allows for 1.6mm to <4mm plate material
- 8 through bolts to mount the plate to the top of the case, M2.5x0.45 head cap screws
- Deck height
- 7mm (height from top of switch plate to top of the case)
- Allows for use of 0.5mm silicone gasket that will make deck-height the ideal 7.5mm to submerge standard keycaps and create a nice aesthetic
- Easy access to mounting screws to easily change out switch plates
- Gaskets (Optional)These are optional but I designed them to help with acoustics with the priority on silencing. I'm still experimenting with the multiple gaskets, switch plate metals and switch+keycap combinations.
- 0.5mm Switch plate gasket between case top and switch plate top. This will recess the switch plate down to hit the ideal 7.5mm depth.
- 2mm or 3mm EVA Foam or 0.5mm silicone PCB gasket to place between the PCB and switch plate to help dampen sound
- 2mm EVA foam to fill the case cavity between the top of the base plate and bottom of the PCB
- 1.5mm silicone gasket to seal entire inside surface of bottom plate to reduce reverberation inside the case. This helps the base plate protrude to create a better aesthetic at the expensve of making the whole case 1.5mm taller
Risks
- Ordering completely custom CNC milled parts in low quantities is expensive
- You will be managing orders from multiple manufactures and vendors so choose wisely
- I provide no warranties or guarantees. Use this information solely at your own risk. I am not liable for any claims, damages, etc.
- If you modify the CAD designs, you will need to know what you're doing and do so at your own risk. These models are provided as-is
- Even if you use these designs and a bad manufacturer, there is a good change you will receive very expensive paper weights
Assets and Materials Needed
Use these files at your own risk*
- Arisu PCB v1.1 for gerber files
- I built custom BOM (Bag Of Materials) and CPL (positioning) files to be used with JLCPCB: https://gist.github.com/overset/bfde44e95b8ca72d8ffed75c40979b75
- CNC milled unibody Case
- case.step STEP file for the case
- case-drawing.pdf drawings for the case
- CNC milled base plate
- base.step STEP file for the base plate
- base-plate_drawing.pdf drawings for the base plate
- laser-cut switch plate
- switch-plate.dxf DXF file for use with laser-cutting services
- machine cut gasket kit for sound dampening (optional)
- gasket_base-plate.dxf gasket that covers the entire inner surface of the base plate and fits in the case flange to help with sound dampening.
- gasket_case-foam-dampener.dxf this is for the case cavity to fill with sound dampener such as EVA foam and is placed in the base between the base plate and PCB
- gasket_pcb.dxf for cutting out a layer of dampener between the switch plate and PCB.
- gasket_switch-plate.dxf for a thin layer of silicone between the switch plate top of the case. Do not go over 0.5mm thickness.
- (Optional) If you would rather get a laser-cut base-plate and not go with CNC for cheaper
- 4x M2.5x0.45 10mm stainless steel countersunk machine screws (I prefer hex)
- 8x M2.5x0.45 6mm stainless steel head cap machine screws (I prefer hex)
Tutorial on Ordering Parts
This is a rough outline of specific vendors I used for the first prototype and should not be treated as an explicit step by step guide. There is great monetary risk with this project and I am not liable for anything you do with this information - see Risks. I have no affiliation with any of the vendors mentioned here and the only bias I have is that I'm pleased with what I've received so far.
The first item to get manufactured was the Arisu PCB v1.1. I used the release assets (gerber files) from Arisu PCB v1.1 and had them manufactured by JLCPCB. Here are a few notes on that process:
- Ordering is easy on JLCPCB using the provided gerber files from FateNozomi
- I opted for SMT Assembly using BOM and CPL files from https://gist.github.com/overset/bfde44e95b8ca72d8ffed75c40979b75 which were exported from the Arisu PCB v1.1 project using KiCad
- Most SMT parts were in stock and supported by their assembly process except the USB connector. I had to source the connector from another vendor directly (DigiKey) and solder it by hand. This was arguably the most difficult component to solder due to how small the pins are - but it's easier with flux and a good soldering iron
- There is a MOQ of 5
- Their turnaround time for me was 5 days at most
- You can only get the default green solder mask if you opt in for SMT assembly
- If you use SMT assembly, be sure to order it for the bottom
The most substantial part of the project was the CNC milling order for the case parts - specifically the "case" and "base plate". I opted to use 3DHubs. The ordering process was easy and here are a few notes on the process:
- They accept the .step files for both the "case" and "base plate" through their online quoting tool
- I created a single order for 2 parts: "case" and "base plate"
- The "case" model did not automatically pass their "Manufacturability Analysis" calling for review on "Thin walls" check but did this was not flagged anywhere else in the process
- I opted for 6061-T6 aluminum on both parts
- For the "case" part
- Surface finish: "Bead Blasted + Anodized type II (Matte)" and added a note in the case drawings to use the finer #150 grit beads for a nicer finish
- Custom color: RAL 7024 Graphite Grey
- "Yes" for "Contains threads"
- For the "base plate" part
- Surface finish "Smoothed + Anodized type II (Glossy)"
- Custom color RAL 7001 Silver Grey (In retrospect, I might have liked the bead blasted matte finish better)
- I uploaded the exhaustive drawings for each part
- It took 2 days for an affiliate in the 3DHubs network to pickup the work
- It took 15 days from order being placed to receiving parts at my door even while opting for longest 20day lead time
The switch plates I opted to use a laser-cutting service SendCutSend. They specialize in metals and do not offer finishing services beyond brushing as of this writing.
- I quickly created quotes using the switch plate .dxf asset and ordered ~1.6mm thick cuts of 6061-T6 Aluminum, 260 Brass, 110 Copper and g5 Titanium. My goal was to test several materials for feel and acoustics as I continue the building process.
- The turn around time is fast with the last order taking 2 days to get to my door
- The cuts were clean and finish was good with minor tooling marks to be expected from any laser-cutting without having finish work done.
- Fitment was good without being overly cautious with kerf. Cherry MX, Zeal and Alpacas fit perfectly on all the plates.
- Through holes have a little room to adjust the plate (0.1mm) just to help with alignment even more.
The gaskets were ordered from Ponoko which can cut EVA foam and Silicone of various thickness. These are very much optional and I have yet to test them
- 0.5mm silicone gasket between the switch plate and case top to help with dampening.
- 1mm silicone and 2mm EVA foam cutouts for dampening between switch plate and PCB
- 2mm and 3mm EVA foam case cavity sound dampening
- 1.5mm silicone base-plate seal that fully covers the interior surface area of the base plate. This also helps the base plate to protrude more from the case to help with aesthetics.
- The ordering process is very straight forward and all gasket assets are compatible
- Ensure that you chose MM and do verify the dimensions before placing your order
- Turn around time is often quick but depends on material stock and demand
Show Me The Build!
First build complete and timelapse video here: https://youtu.be/O6BLock8iVU
Typing test for the first build here: https://youtu.be/mfLEsenbGh8
Some details on the build:
- Case is a Unibody CNC 6061-T6 Aluminum top, sandblasted with fine grit, anodized Graphite Grey
- Bottom case plate is CNC 6061-T6 Aluminum smoothed and anodized Silver Grey
- Switch plate is 1.6mm 260 Brass
- 0.5mm silicone machine-cut switch plate to case gasket
- 2mm EVA foam machine-cut dampener between PCB and switch plate
- 2mm EVA foam machine-cut for case cavity between PCB and base plate
- 1.5mm silicone base-plate gasket
- Switches are Silent Alpacas + TX Film + 205g0 lube
- 4x 2U Zeal screw-in Stabilizers + 205g0
- GMK Oblivion V2 Monochrome
I want to make changes to the case!
TODO
- HOWTO navigate parts, assembly and drawings
- Want to change the typing angle?
- How to extract specific assets for manufacturers
FAQ
- Again, Why?I really like the Arisu layout and there is no easily accessible high quality case available for it that meets the aesthetic I was looking for or is something that would be attainable without waiting months if not years. Also: the challenge of building a custom case from scratch
- Why not build another Alice clone case or buy one of r/mm?None of the recent group buys for custom Alice-clone cases have really hit the mark for me aesthetically. I have no doubt the build quality on some, if not all of them, far exceeds this - but the recent surge of interest has made access to join GBs prohibitive. The more recent Prime_E and Rukia come to mind and look amazing. When getting into that price point I'm looking for very specific things such as: a number row (which the Prime_E doesn't have but the upcoming PrimeKB Meridian will have), Arrow keys are a must (not on the Alice or Rukia and no number of custom layers or HJKL bindings are going to save that for me)
- RGB? ISO? Rotary Encoders? Extra B?No, No, No and No
- But it's not symmetrical like the Alice, why waste your money?This actually does not bother me at all. Having spend so many years on 75%, TKL and Fullsize keyboards I've always had the majority of keys on the right side. I just expect it and if it's too symmetrical it doesn't feel right to me. Even the Alice is not perfectly symmetrical
- When is the GB?Right now, I do not intend on running a GB myself. I'm licensing the work here in a way that does not prohibit it. If you want to run a group by or one on derived work and use OnShape do consider their ToS. Also, add a reference for this and the amazing work from FateNozomi for the original Arisu keyboard. I'm happy to consult as my time allows on derivative work - it's at the heart of opensource after all
- Any modifications required to the Arisu PCB?None. This is designed around the stock Arisu v1.1 PCB.
- Will you sell me one for $100No
- How much will this cost?Low volume CNC work is cost prohibitive, but not astronomical. This varies greatly depending on manufacturers selected, finishes chosen, etc.
- Where is the wrist rest?See TODO
- Why OnShape and not Solidworks, Fusion360?
- It's completely free
- It's parametric CAD
- It's feature rich and easy to use with a short learning curve
- I have not found any missing functionality I thought I would need in the modeling of this case
- The Drawings interface is very powerful
- You can fork my design and change whatever you want
- Did I mention it's completely free?
TODO
- Wrist rest! I have a stacked acrylic prototype that I'm already using and love. I have a design for laser-cut solid maple with a leather top to fit perfectly with the case design. I might consider a solid polycarbonate version in the future similar to many other designs I've seen in the community and update this project appropriately
- CNC simplification and cost cutting
- Reduce reliance on microtooling such as larger fillets
- Larger radii of inner cutouts in the case - they're likely less than the standard 1/4 diameter of main cutting tool
- More consistent fillets and radii to minimize different bits or bit changes
- Add fillet to bottom of recessed logo on base plate - this cannot be a sharp corner
- Add more through bolts to the base plate for an even more secure design. The 4 bolt pattern is still more than enough
- Consider raising the deck height of the top of the case from 7mm to 7.5 to account for proper clearance of standard keycaps. The 7mm design was originally built to incorporate a 0.5mm silicone gasket to help dampen sound, but this might not be desirable for some.
- Make the USB port hole a little more centered and the access hole smaller. Possibly add a chamfer, fillet, etc to the USB port more visually appealing
- Experiment with adding more material to the baseplate to bring it parallel with the PCB and minimize the volume of open air inside the case. The intent would be to benefit acoustics and add more weight to the keyboard. I'm very satisfied with the gasket dampener kit as part of the original design for helping with the acoustics
- Test more base plate materials such as various brass, copper, polished stainless, etc. I've started a new OnShape branch for this at JP01 - CNC Unibody Case - Arisu Keyboard brass baseplate
- Add another switch plate screw near the bottom right corner to prevent extra flex when pressing on the right arrow key. This was not even noticeable with the 1.6mm brass, copper, titanium or 6061-T6 aluminum plates I was testing with but would make it closer to perfect
- This design should work with Polycarbonate and getting a prototype milled is on the list
- Explore finishing options for switch plates (i.e. PVD)
- Clean up OnShape project, unused Sketches, add variables for typing angle with constraints, make easier to export parts, optimize drawings
- Bumpons
Credits
This case was inspired by FateNozomi's Arisu PCB and Arisu Case which was inspired by Lyn's EM7 and the fabled TGR Alice. This is referred to as the "open source Alice with arrows" and now with a solid unibody case.